cast or forged ??
#16
Really....I thought all factory wheels are forged....I have a both Carrera S II and Turbo Wheel....are both cast?
#17
I was under the impression that factory wheels were forged also. I read something on the PCA tech site and figured they knew what they were talking about. When I swapped my factory wheels for the Rugers and had to haul the lobsters around sans tires......forged boat anchors? The lobsters seemed really heavy.
#20
There is no question that a forged wheel is superior to a cast wheel. A forged wheel will always be lighter than its cast counterpart, and most of the time significantly stronger. It comes down to the manufacturing processes- the forged material has significantly greater strength properties which allows you to use less material to achieve the same load rating.
While there are some quality cast wheels out there (Forgestar, BBS, etc), 95% of it is absolute junk. Most of the "replica" cast wheels are all junk (let alone boat anchors in terms of weight). Think about it this way- why would you want to put a wheel on your car that is of LESSER quality than your OEM wheels? That is what I tell all of my customers.
If you are on a budget, stick to a quality cast wheel from a reputable brand. Trust me when I say this that you really don't know what you are getting with the majority of the cast wheels on the market (especially the replicas). As I mentioned above, BBS or Forgestar are safe choices.
Hope this helps.
While there are some quality cast wheels out there (Forgestar, BBS, etc), 95% of it is absolute junk. Most of the "replica" cast wheels are all junk (let alone boat anchors in terms of weight). Think about it this way- why would you want to put a wheel on your car that is of LESSER quality than your OEM wheels? That is what I tell all of my customers.
If you are on a budget, stick to a quality cast wheel from a reputable brand. Trust me when I say this that you really don't know what you are getting with the majority of the cast wheels on the market (especially the replicas). As I mentioned above, BBS or Forgestar are safe choices.
Hope this helps.
#21
I love these thread, they give us the opportunity to inform the customers on the various options in the wheel industry - a complex industry!
Below is an article written by Carlos, lead engineer at MORR wheels, on all you need to know in the wheel manufacturing industry. You can combine flow forming with a cast or forged wheel to make a "hybrid". The MORR VS8.1 1 piece forged wheels have flow formed barrels for reduced weight. The Forgestars are a cast hybrid with flow formed barrels. They are our number one choice for lightweight, high quality, well priced wheels.
Below is an article written by Carlos, lead engineer at MORR wheels, on all you need to know in the wheel manufacturing industry. You can combine flow forming with a cast or forged wheel to make a "hybrid". The MORR VS8.1 1 piece forged wheels have flow formed barrels for reduced weight. The Forgestars are a cast hybrid with flow formed barrels. They are our number one choice for lightweight, high quality, well priced wheels.
This information comes from over 5 years of experience in the automotive wheel industry. I’m an Industrial Engineer with a minor in Mechanical Design, I own two wheel companies, have dealt with every aftermarket forged wheel manufacturer in the world, have designed, engineered and manufactured very strong and light wheels in both cast and forged variants and have very close relationships with some of the leaders of the wheels industry in the USA including members of the SAE Aftermarket Wheel Committee and the SEMA Wheel Industry Council.
Here is the first article. Hope you like it and could use it to form accurate opinions about your future wheel purchase and can properly and accurately assist others.
Alloy wheels, or most commonly known as “rims” are automobile wheels that are manufactured from aluminum or magnesium alloy metals. They are called alloy wheels since they are not manufactured from pure aluminum or magnesium but using alloys (mix of metals) usually 6000-Series for high end aluminum wheels which contains less than 1% Si and about 1% magnesium.
6060-T6 Aluminum is very good because of its properties. It is very ductile, durable and lightweight, making it very good among wheel manufacturers. The “T6” comes from a Heat Treatment technique called precipitation hardening and an artificially aging process to alter the properties of the alloy
Automotive wheels can be manufactured using several process. Setian (DTMRack.com) and crimsone90 made very good articles referring these methods. This articles can be found here (http://www.m3post.com/forums/showthread.php?t=357430) and here: (http://www.e90post.com/forums/showthread.php?t=295274).
Casting
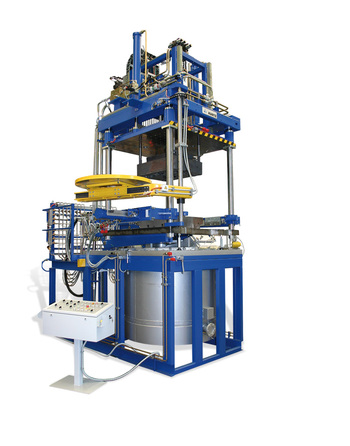
Most of you are familiar with this process.
By definition, “Casting is a manufacturing process by which a liquid material is usually poured into a mold, which contains a hollow cavity of the desired shape, and then allowed to solidify.” There are two main techniques to cast aluminum wheels, gravity casting and low-pressure casting.
Gravity casting is a method of manufacturing a cast wheel of an specific metal alloy, typically aluminum, although Magnesium is also used, which involves supplying molten metal to a mould cavity via a feeder through a running system where the molten metal entry point is located above the top of the mould cavity. In this manufacturing process all the metal entering the mould is subject to turbulence. This turbulence can cause severe defects such as oxide inclusions and entrapped gas porosity and in some cases mould erosion and hotspots.
Low-pressure casting in the other hand takes care of the disadvantages of Gravity casting by filling the mould by injecting molten metal at about 25psi through an in-gate just below the top of the mould cavity from a source under the mould through a method which allows complete filling of the mould. The force of gravity acts against the upward flow of the metal and eliminates the possible turbulence caused by the falling liquid metal. The molten metal is stored in a pressured container and by increasing the pressure metal is then forced into the mould.
In low-pressure casting the method in which the metal is forced into the mould is the main difference/advantage over gravity casting and is absolutely controlled. As explained above it results in a low turbulence or turbulence-free mould filling with little to no corrosion.
The molten metal in the furnace is in a closed container under protected atmosphere. Because of this the metal absorbs less hydrogen and any other impurities as well as the oxide formation being greatly reduced. As opposed to gravity casting, the metal surface is not interrupted constantly since it is been forced from under the metal surface. What you get is a very clean quality metal.
Basically low-pressure casting uses positive pressure to move molten metal into the mold quickly thus resulting in a finished product with an Aluminum that is denser than Gravity cast.
The advantages of low pressure die casting process are several:
- higher yield achievable
- reduction of machining costs
- excellent control of process parameters
- good metallurgical quality
- leads to an optimal use of the aluminum
- excellent mechanical and technological properties of the castings.
Forging:

Out of the three, Forging is the manufacturing process that creates the lightest metals. There are several ways to forge alloy wheels, but the most common is press forging.
By definition “Forging is the shaping of metal using localized compressive forces. It is to form or to make by heating and pressing.”
The forging process uses immense amounts of compressive force to shape the metal. During this process a wheel blank is placed between two shaped plates and the press slowly shapes the wheel using continuous forces. During the process the internal grain is deformed and rearranged to the shape of the part. This deformation due to compressive force improves the strength uniformly throughout the entire structure of the wheel. Press Forging allows closer tolerances as well. The wheel is typically heated to about 400-Farenheit. The forging process typically uses anything between 4,000 to 10,000 tons of pressure, 6000 being the most common, and reaches up to 16,000 tons to produce forged magnesium wheels. Heat treatment and artificial aging can further improve the wheel mechanical properties.
It is important to understand that forging does not compress the metal. Forging alters the grain structure of the metal and makes it stronger. For example, a 19” aluminum wheel blank that weights 30lbs will still weight 30lbs after the forging process. The major difference is that after the forging process, the 30lbs forged aluminum wheel blank will be much stronger. Since the aluminum is stronger it allows the engineers to manufacture a lighter wheel by removing excess aluminum.
To make it easier to understand, imagine a structure that requires a beam with a diameter of 5-inches. If we manufacture that beam out of forged aluminum, since the mechanical properties have been improved, the beam diameter could now be reduced to around 2-3” in diameter helping to make the structure lighter. You could do the same and keep the diameter of the beam at 5-inches if your purpose is to make it stronger.
In other words, Forging does not make the metal lighter, it makes it stronger. Forged wheels are also formed via flow-forming which is explained below.
Flow-Forming:

Flow Forming is a precision metal forming. It is commonly known as a forming technique. It is the newest player and is only available by a limited number of manufacturer.
By definition: “Flow Forming is an incremental metal forming technique in which a disk or tube of metal is formed over a mandrel by one or more rollers using tremendous pressure.”
In other words, a disk, or in this case an aluminum wheel blank, is placed between two rollers and the wheel spins while the two rollers form the barrel at high pressures and extends the barrel of the wheel to the desired length. This deformation arranges the grain structure of the metal in the direction of the rotation of the wheel. The blank is typically made using metal casting. This process helps reduce barrel thickness. The blank barrel is usually around 4.0-9.0-inches wide and is extended to 7.0”-11.0-inches depending on the application. Although the piece is cold formed, during the forming process, due to friction, the wheel blank is heated to around 400-Farenheit. Because of the high pressure and high temperature the metal mechanical properties are changed. The mechanical properties of the metal became very similar, if not the same, to that of a forged wheel. No material is lost during the forming process, resulting in less aluminum used to create the finished wheel.
Flow Forming in essence forges the wheel barrel by spinning and forming. Forming can be done hot, warm or cold and is accomplished on mechanical or hydraulic press, or on special forming equipment. Heat treatment and artificial aging can further improve the wheel mechanical properties. Flow forming process can be a cost-effective alternative to conventional press forging.
Because of its properties flow forming is also known as liquid forging.
Article 1
Here is the first article. Hope you like it and could use it to form accurate opinions about your future wheel purchase and can properly and accurately assist others.
What are Alloy Wheels?
Alloy wheels, or most commonly known as “rims” are automobile wheels that are manufactured from aluminum or magnesium alloy metals. They are called alloy wheels since they are not manufactured from pure aluminum or magnesium but using alloys (mix of metals) usually 6000-Series for high end aluminum wheels which contains less than 1% Si and about 1% magnesium.
6060-T6 Aluminum is very good because of its properties. It is very ductile, durable and lightweight, making it very good among wheel manufacturers. The “T6” comes from a Heat Treatment technique called precipitation hardening and an artificially aging process to alter the properties of the alloy
Manufacturing:
Automotive wheels can be manufactured using several process. Setian (DTMRack.com) and crimsone90 made very good articles referring these methods. This articles can be found here (http://www.m3post.com/forums/showthread.php?t=357430) and here: (http://www.e90post.com/forums/showthread.php?t=295274).
Casting
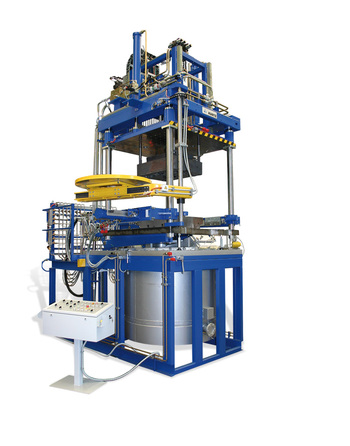
Most of you are familiar with this process.
By definition, “Casting is a manufacturing process by which a liquid material is usually poured into a mold, which contains a hollow cavity of the desired shape, and then allowed to solidify.” There are two main techniques to cast aluminum wheels, gravity casting and low-pressure casting.
Gravity casting is a method of manufacturing a cast wheel of an specific metal alloy, typically aluminum, although Magnesium is also used, which involves supplying molten metal to a mould cavity via a feeder through a running system where the molten metal entry point is located above the top of the mould cavity. In this manufacturing process all the metal entering the mould is subject to turbulence. This turbulence can cause severe defects such as oxide inclusions and entrapped gas porosity and in some cases mould erosion and hotspots.
Low-pressure casting in the other hand takes care of the disadvantages of Gravity casting by filling the mould by injecting molten metal at about 25psi through an in-gate just below the top of the mould cavity from a source under the mould through a method which allows complete filling of the mould. The force of gravity acts against the upward flow of the metal and eliminates the possible turbulence caused by the falling liquid metal. The molten metal is stored in a pressured container and by increasing the pressure metal is then forced into the mould.
In low-pressure casting the method in which the metal is forced into the mould is the main difference/advantage over gravity casting and is absolutely controlled. As explained above it results in a low turbulence or turbulence-free mould filling with little to no corrosion.
The molten metal in the furnace is in a closed container under protected atmosphere. Because of this the metal absorbs less hydrogen and any other impurities as well as the oxide formation being greatly reduced. As opposed to gravity casting, the metal surface is not interrupted constantly since it is been forced from under the metal surface. What you get is a very clean quality metal.
Basically low-pressure casting uses positive pressure to move molten metal into the mold quickly thus resulting in a finished product with an Aluminum that is denser than Gravity cast.
The advantages of low pressure die casting process are several:
- higher yield achievable
- reduction of machining costs
- excellent control of process parameters
- good metallurgical quality
- leads to an optimal use of the aluminum
- excellent mechanical and technological properties of the castings.
Forging:

Out of the three, Forging is the manufacturing process that creates the lightest metals. There are several ways to forge alloy wheels, but the most common is press forging.
By definition “Forging is the shaping of metal using localized compressive forces. It is to form or to make by heating and pressing.”
The forging process uses immense amounts of compressive force to shape the metal. During this process a wheel blank is placed between two shaped plates and the press slowly shapes the wheel using continuous forces. During the process the internal grain is deformed and rearranged to the shape of the part. This deformation due to compressive force improves the strength uniformly throughout the entire structure of the wheel. Press Forging allows closer tolerances as well. The wheel is typically heated to about 400-Farenheit. The forging process typically uses anything between 4,000 to 10,000 tons of pressure, 6000 being the most common, and reaches up to 16,000 tons to produce forged magnesium wheels. Heat treatment and artificial aging can further improve the wheel mechanical properties.
It is important to understand that forging does not compress the metal. Forging alters the grain structure of the metal and makes it stronger. For example, a 19” aluminum wheel blank that weights 30lbs will still weight 30lbs after the forging process. The major difference is that after the forging process, the 30lbs forged aluminum wheel blank will be much stronger. Since the aluminum is stronger it allows the engineers to manufacture a lighter wheel by removing excess aluminum.
To make it easier to understand, imagine a structure that requires a beam with a diameter of 5-inches. If we manufacture that beam out of forged aluminum, since the mechanical properties have been improved, the beam diameter could now be reduced to around 2-3” in diameter helping to make the structure lighter. You could do the same and keep the diameter of the beam at 5-inches if your purpose is to make it stronger.
In other words, Forging does not make the metal lighter, it makes it stronger. Forged wheels are also formed via flow-forming which is explained below.
Flow-Forming:

Flow Forming is a precision metal forming. It is commonly known as a forming technique. It is the newest player and is only available by a limited number of manufacturer.
By definition: “Flow Forming is an incremental metal forming technique in which a disk or tube of metal is formed over a mandrel by one or more rollers using tremendous pressure.”
In other words, a disk, or in this case an aluminum wheel blank, is placed between two rollers and the wheel spins while the two rollers form the barrel at high pressures and extends the barrel of the wheel to the desired length. This deformation arranges the grain structure of the metal in the direction of the rotation of the wheel. The blank is typically made using metal casting. This process helps reduce barrel thickness. The blank barrel is usually around 4.0-9.0-inches wide and is extended to 7.0”-11.0-inches depending on the application. Although the piece is cold formed, during the forming process, due to friction, the wheel blank is heated to around 400-Farenheit. Because of the high pressure and high temperature the metal mechanical properties are changed. The mechanical properties of the metal became very similar, if not the same, to that of a forged wheel. No material is lost during the forming process, resulting in less aluminum used to create the finished wheel.
Flow Forming in essence forges the wheel barrel by spinning and forming. Forming can be done hot, warm or cold and is accomplished on mechanical or hydraulic press, or on special forming equipment. Heat treatment and artificial aging can further improve the wheel mechanical properties. Flow forming process can be a cost-effective alternative to conventional press forging.
Because of its properties flow forming is also known as liquid forging.
Last edited by CampioniShop1; 02-23-2012 at 03:47 PM.
#22
Very nice information here and objective.
I've been buying custom wheels for over 25 years and I don't consider forged to be superior over cast wheels. Forged most often looks better and that is enough to select them in most ocassions.
It all depends on what you want. If you are doing a lot of performance driving you want the lightest strongest wheel possible. That would be a forged monoblock wheel. If you are endurance racing, I would prefer a cast monoblock that is not too large. The thicker metal would provide strength and the smaller diameter is good for rapid acceleration and deceleration. Big wheels (19, 20, 21, 22) are better for maintaining high speed but take longer to get there and longer to stop.....but they use less energy to maintain high speeds. So these are better for drag racing.
I could go on about different applications but you all get the point.
What I hate is some dealers who try to convince people to buy 3 piece forged wheels claiming that is the best possible choice when all they want is for you to spend the most possible coin.
The dealer really ask about your driving style, the normal conditions for the wheel's use, your price range, etc....then match your needs to a wheel.
I've been buying custom wheels for over 25 years and I don't consider forged to be superior over cast wheels. Forged most often looks better and that is enough to select them in most ocassions.
It all depends on what you want. If you are doing a lot of performance driving you want the lightest strongest wheel possible. That would be a forged monoblock wheel. If you are endurance racing, I would prefer a cast monoblock that is not too large. The thicker metal would provide strength and the smaller diameter is good for rapid acceleration and deceleration. Big wheels (19, 20, 21, 22) are better for maintaining high speed but take longer to get there and longer to stop.....but they use less energy to maintain high speeds. So these are better for drag racing.
I could go on about different applications but you all get the point.
What I hate is some dealers who try to convince people to buy 3 piece forged wheels claiming that is the best possible choice when all they want is for you to spend the most possible coin.
The dealer really ask about your driving style, the normal conditions for the wheel's use, your price range, etc....then match your needs to a wheel.
Last edited by ice350; 02-23-2012 at 08:26 PM.
#23
Carlos' write-up was very informative.
However, some very relevant info was not included in the article.
Flow-forming does, in fact, add strength properties to the alloy in the BARREL area. However, there is very little load in the barrel of any wheel, cast or forged. The barrel does hardly more than hold air.
Any competent wheel engineer knows this. And FEA stress analysis shows this in every case.
The majority of the load carrying in any wheel is accomplished by the face (spokes) of the wheel. Flow-forming does nothing to improve the grain structure or alloy strength in this critical area.
So, in my opinion, suggesting that a cast/flowformed wheel is similar in quality to a forged wheel is deceptive and disingenuous.
There are some good quality flow formed wheels on the market, no question. But they are cast wheels and no amount of marketing hype changes that fact.
However, some very relevant info was not included in the article.
Flow-forming does, in fact, add strength properties to the alloy in the BARREL area. However, there is very little load in the barrel of any wheel, cast or forged. The barrel does hardly more than hold air.
Any competent wheel engineer knows this. And FEA stress analysis shows this in every case.
The majority of the load carrying in any wheel is accomplished by the face (spokes) of the wheel. Flow-forming does nothing to improve the grain structure or alloy strength in this critical area.
So, in my opinion, suggesting that a cast/flowformed wheel is similar in quality to a forged wheel is deceptive and disingenuous.
There are some good quality flow formed wheels on the market, no question. But they are cast wheels and no amount of marketing hype changes that fact.
#24
Didn't some people in the past refer to the SSR wheel as a Seriuosly Soft Rim? The SSR was one of the first flow formed wheels.
I'd rather have a Porsche cast wheel on my car over any flow formed after market wheel.
I'd rather have a Porsche cast wheel on my car over any flow formed after market wheel.
#25
It is only called SSF in the automotive industry (marketing?), elsewhere it is known as semi-solid metal casting.
The word "forge" has no legal definition and therefore is widely abused and misinterpreted.
Forging imparts exceptional qualities to metals but is quite expensive. A typical forging needed for a 20 lb 19 inch wheel, weighs as much as 90-100 lbs. During the many manufacturing processes, the forging is machined to its finished weight. These scrap costs and machining costs contribute heavily to the premium prices of forged wheels in the market.
Cast/flow-formed and SSF wheels have little waste because they are not forgings at all.

#26
I think you are right but the weight difference really isn't that great. I have cast Carrera Sports and I found the following weight comparison with the forged Turbos:
Porsche Factory Carrera Sport - 106 lbs, 12 oz.
8.5x19" 24 lbs. 2 oz.
11.5x19" 29 lbs. 4 oz.
Forged Turbo Wheels - 102 lbs, 12 ozs.
8.5x19" 23 lbs. 8 oz
11x19" 27 lbs. 14 oz.
As for strength, I've tracked my car, A/X'd my car, and hit more Washington, DC, potholes than I can count and my "weaker" cast wheels don't have so much as a scratch.
Porsche Factory Carrera Sport - 106 lbs, 12 oz.
8.5x19" 24 lbs. 2 oz.
11.5x19" 29 lbs. 4 oz.
Forged Turbo Wheels - 102 lbs, 12 ozs.
8.5x19" 23 lbs. 8 oz
11x19" 27 lbs. 14 oz.
As for strength, I've tracked my car, A/X'd my car, and hit more Washington, DC, potholes than I can count and my "weaker" cast wheels don't have so much as a scratch.
#27
I think you are right but the weight difference really isn't that great. I have cast Carrera Sports and I found the following weight comparison with the forged Turbos:
Porsche Factory Carrera Sport - 106 lbs, 12 oz.
8.5x19" 24 lbs. 2 oz.
11.5x19" 29 lbs. 4 oz.
Forged Turbo Wheels - 102 lbs, 12 ozs.
8.5x19" 23 lbs. 8 oz
11x19" 27 lbs. 14 oz.
As for strength, I've tracked my car, A/X'd my car, and hit more Washington, DC, potholes than I can count and my "weaker" cast wheels don't have so much as a scratch.
Porsche Factory Carrera Sport - 106 lbs, 12 oz.
8.5x19" 24 lbs. 2 oz.
11.5x19" 29 lbs. 4 oz.
Forged Turbo Wheels - 102 lbs, 12 ozs.
8.5x19" 23 lbs. 8 oz
11x19" 27 lbs. 14 oz.
As for strength, I've tracked my car, A/X'd my car, and hit more Washington, DC, potholes than I can count and my "weaker" cast wheels don't have so much as a scratch.
Just make sure they are really forged.
#28
The Alloys
Another key factor in comparing forged and cast/flowformed wheels is the alloy used.
Most cast wheels use an alloy called A356. This is a high-silicon alloy that flows very well when melted, making it ideal for casting aluminum wheels.
Most forged wheels are made from 6061 Alloy, heat-treated to T6.
6061 is a much stronger aluminum alloy than A356. It has superior tensile strength, superior yield strength, higher elasticity and higher Brinell hardness.
These properties enable the alloy to withstand higher loads and greater impacts without damage.
This makes it ideal for forged wheels.
So, to make an informed decision, you need to know BOTH the alloy used and the processes utilized during manufacturing. In addition, it is important to understand the skill, experience and credentials of the engineers who designed the wheel and evaluated its fitness for a particular application.
Most cast wheels use an alloy called A356. This is a high-silicon alloy that flows very well when melted, making it ideal for casting aluminum wheels.
Most forged wheels are made from 6061 Alloy, heat-treated to T6.
6061 is a much stronger aluminum alloy than A356. It has superior tensile strength, superior yield strength, higher elasticity and higher Brinell hardness.
These properties enable the alloy to withstand higher loads and greater impacts without damage.
This makes it ideal for forged wheels.
So, to make an informed decision, you need to know BOTH the alloy used and the processes utilized during manufacturing. In addition, it is important to understand the skill, experience and credentials of the engineers who designed the wheel and evaluated its fitness for a particular application.
#29
its not rocket science..
u just want the looks ?
get the solid-quality cast wheels and save some money.
looking for performance ?
get the lightest wheels u can afford.
Most likely, it will be forged.
no one is claiming forged wheels are stronger than cast wheels..
if u hit the curb hard enough, the rim will bend or break.. cast or forged.
however, most forged wheels will save u substantial weight in the corners and still offer high-strength.. which results in lower unsprung weight (search)
how many cast wheels do u see in the GrandAm or ALMS ?
(yeah, i know we are not professionals.. just trying to point out the importance of unsprung weight.
)
u just want the looks ?
get the solid-quality cast wheels and save some money.
looking for performance ?
get the lightest wheels u can afford.
Most likely, it will be forged.
no one is claiming forged wheels are stronger than cast wheels..
if u hit the curb hard enough, the rim will bend or break.. cast or forged.
however, most forged wheels will save u substantial weight in the corners and still offer high-strength.. which results in lower unsprung weight (search)
how many cast wheels do u see in the GrandAm or ALMS ?

(yeah, i know we are not professionals.. just trying to point out the importance of unsprung weight.

#30
Tech1_Mike hit on the head.
Who designed the wheel and from what knowledge base?
If it is a cast wheel how well is the chemistry controlled on the alloy and how well is the subsequent solution and aging process controlled.
There are places in this world I wouldn't want a wheel from in today's market.
Who designed the wheel and from what knowledge base?
If it is a cast wheel how well is the chemistry controlled on the alloy and how well is the subsequent solution and aging process controlled.
There are places in this world I wouldn't want a wheel from in today's market.